Chemical looping of biomass shows potential as ‘carbon negative’ energy solution
New study shows technique leads to 3.5 times faster reaction rate and more complete combustion
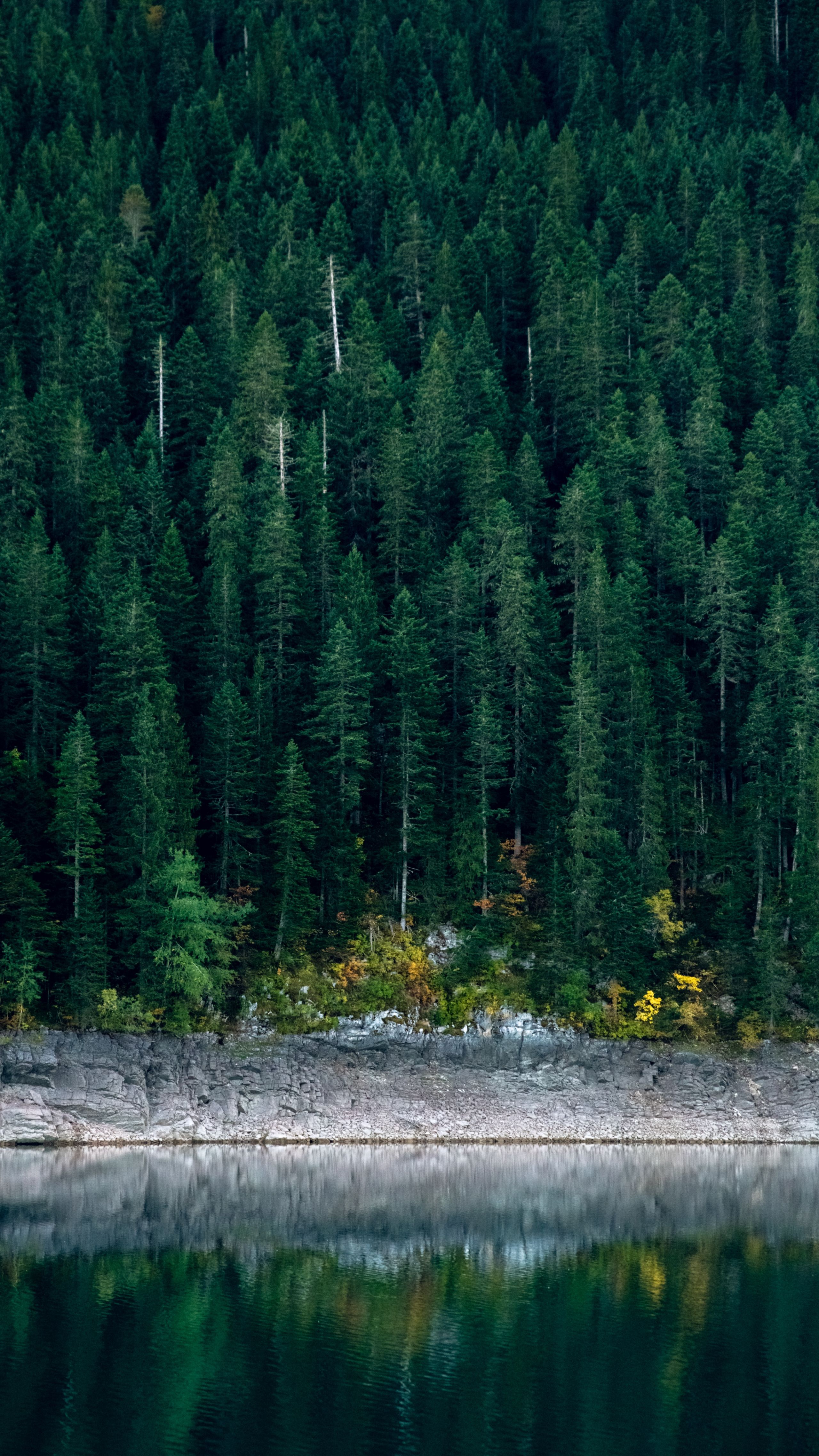
In 2018, driven by increasing demand for energy worldwide, global energy-related carbon dioxide emissions rose by 1.7%, to an historic high of 33.1 gigatonnes. The amount of CO2 in the atmosphere averaged around 407 parts per million that year.
While there has been growth in the use of renewable and carbon-neutral energy sources, the effects of this are not enough to drop atmospheric CO2 concentration to the level needed to avoid some of the disastrous consequences of global warming.
To mitigate these issues there is increasing focus on carbon capture and storage technology, that actively removes CO2 from the atmosphere. But what happens when you combine an already carbon neutral energy source, with carbon capture technology that itself is not energy intensive?
Meet the new aspirational standard in energy generation: carbon negative.
Burning biomass to produce energy has played an important role in reducing our dependency on fossil fuel sources and is considered ‘carbon neutral’.
Trees and plants absorb carbon dioxide from the atmosphere over the course of their lifetime for use in photosynthesis, and when they die and rot down, that carbon dioxide is released back into the atmosphere. By intercepting this process, we can extract energy from the plant matter without creating a net increase in atmospheric carbon dioxide.
But a new study, from researchers in the Energy Reactions and Carriers group at CEB, demonstrates the potential to take the process one step further.
The group’s research focuses on a technique called chemical looping combustion – a method of ‘burning’ material by reacting it with an oxygen carrier, rather than air from the environment.
The biomass is added to a reactor with the oxygen carrier – a chemical compound, often a metal oxide – which releases oxygen directly to the fuel, causing a combustion reaction that generates energy. The depleted carrier can be removed from the reactor and re-oxidised in air, ready to be used again, in a cyclical system.
Diagram of a typical chemical looping combustion set up with a copper (II) oxide oxygen carrier
Diagram of a typical chemical looping combustion set up with a copper (II) oxide oxygen carrier
The advantage of using chemical looping to burn your fuel, is that the carbon dioxide released from the combustion reaction can be captured directly and doesn’t need to be separated from the air in which the fuel is burnt, as in traditional combustion reactors.
A major barrier to the viability of carbon capture and storage technologies is the energy required to separate carbon dioxide from the other gases in air, predominantly nitrogen.
This separation is, at the moment, incredibly energy-intensive and is often cited as a major drawback of carbon capture technologies.
If the process to capture the carbon dioxide itself requires vast amounts of energy, then any environmental gains from the process are significantly diminished.
Using chemical looping, no separation is needed as there’s no air involved in the first place: the carbon dioxide can simply be collected straight from the reactor and passed directly to your chosen storage method, or even used as a reactant in future chemical processes.
"Chemical looping combustion with oxygen uncoupling has been studied for energy production for about 10 years now, yet Kenny is the first to derive an analytical solution for the process and quantitatively discuss arising enhancement effects".
The new study from our Combustion Group demonstrates the chemical looping combustion of biomass char and presents some even more promising findings.
They discovered that compared with burning the biomass char in air, chemical looping leads to a more complete combustion process. Often in combustion reactors, rather than the reaction proceeding efficiently to completion, and producing only carbon dioxide and water, there will be incomplete reactions that lead to the formation of carbon monoxide and soots.
These are again difficult to separate out from the other products and cause further complications for carbon capture methods.
In the chemical looping set up, the researchers saw virtually no carbon monoxide in the off gas, indicating a much more efficient process.
Not only that, but the rate of the reaction was significantly increased.
“Very surprisingly, the rate of reaction is much faster with chemical looping,” explains Kenny Kwong, a third year PhD student in the Combustion Group. “If you look at how long it takes to burn the same size of biomass particle in air, the chemical looping combustion set up is three and a half times faster.”
To find an explanation for this, the researchers set about solving the problem analytically.
“Often to explain experimental results, researchers will use mathematical or numerical models of the system,” says Kwong.
“But if we have the analytical solutions, we are able to explain the science behind it and that allows us to optimise the reaction more easily, at a lower combinational cost.”
They found that it is the improved mass transfer afforded by chemical looping that makes the reaction so much faster.
Graphical abstract taken from Kwong, K.; Mao, R.; Scott, S.; Dennis, J.; Marek, E. Analysis of the Rate of Combustion of Biomass Char in a Fluidised Bed of CLOU Particles. Chemical Engineering Journal 2020, 127942.
Graphical abstract taken from Kwong, K.; Mao, R.; Scott, S.; Dennis, J.; Marek, E. Analysis of the Rate of Combustion of Biomass Char in a Fluidised Bed of CLOU Particles. Chemical Engineering Journal 2020, 127942.
When you burn the biochar particle in air, any oxygen in the air that is close to the particle will be consumed, so the concentration of oxygen at the surface of the particle is very low.
With an oxygen carrier, because the carrier itself is in close contact with the char particle, it can continually release oxygen to the surface, replenishing any oxygen consumed in the reaction. This ensures the oxygen concentration at the biochar particle surface remains consistently high, increasing the reaction rate.
"Chemical looping combustion with oxygen uncoupling has been studied for energy production for about 10 years now," explains Dr Ewa Marek, who leads our Combustion Group. "Yet, Kenny is the first to derive an analytical solution for the process and quantitatively discuss arising enhancement effects".
The researchers now want to study the interactions between the biochar particle and the oxygen carrier in more depth, particularly regarding any incomplete combustion reactions producing carbon monoxide, that could reduce the efficiency of oxygen transfer.
“The more understanding we have of the science behind this reaction process, the more easily we can predict performance and improve the efficiency," says Kwong.
“I really want to thank the members of my group and the technicians in the department – especially Chris Bawden – who have done a lot of work on restructuring the rig to make these experiments possible.”
While this combination of processes has great potential to provide carbon negative energy solutions, there is still more work to be done to enable its uptake across the energy industry.
“To use chemical looping potentially requires restructuring your power plant and there are obviously costs involved in this,” says Kwong. “That’s why this research is so important, because we are providing analytical solutions that help us to understand the science behind the process and can accelerate the technology-readiness.”
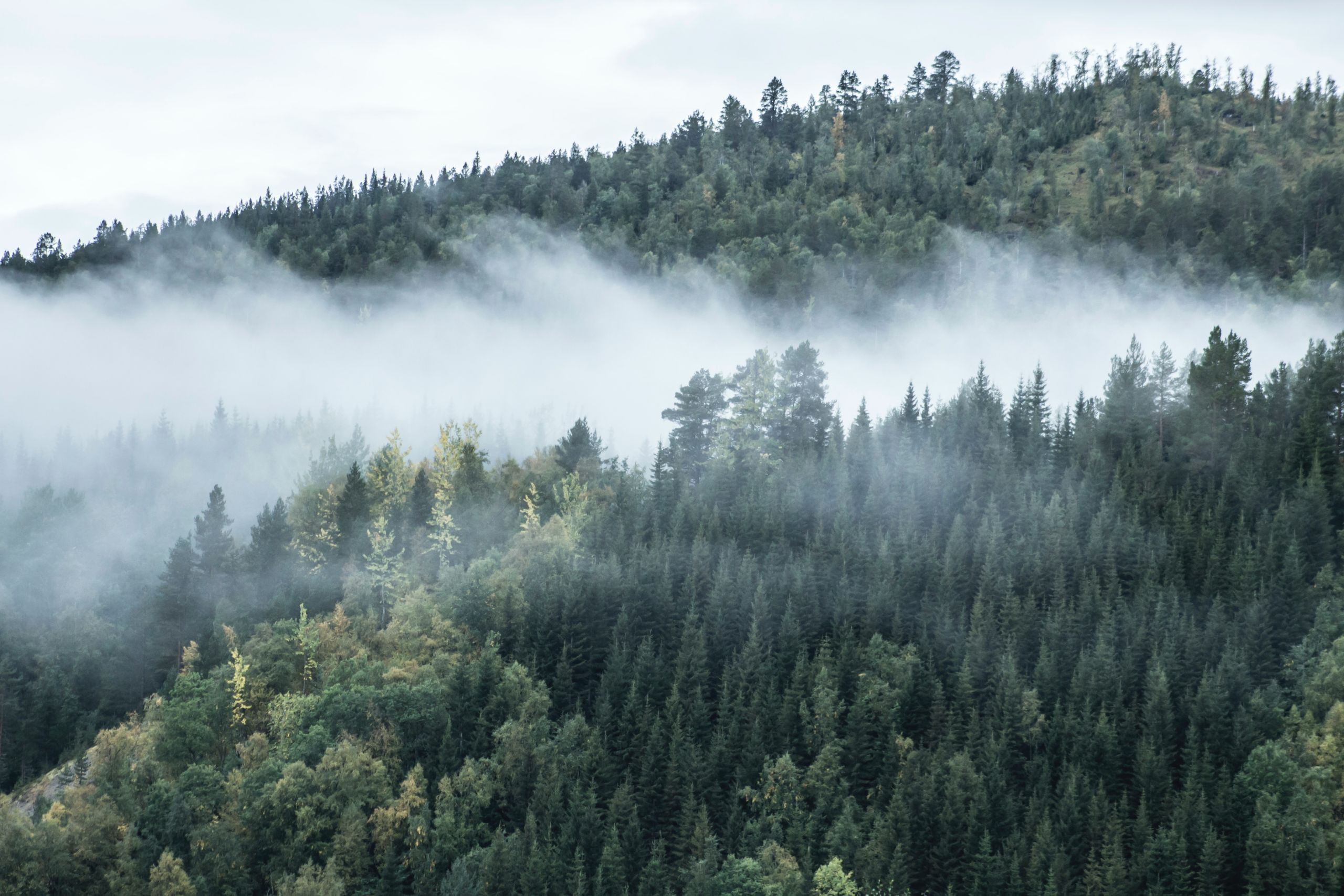
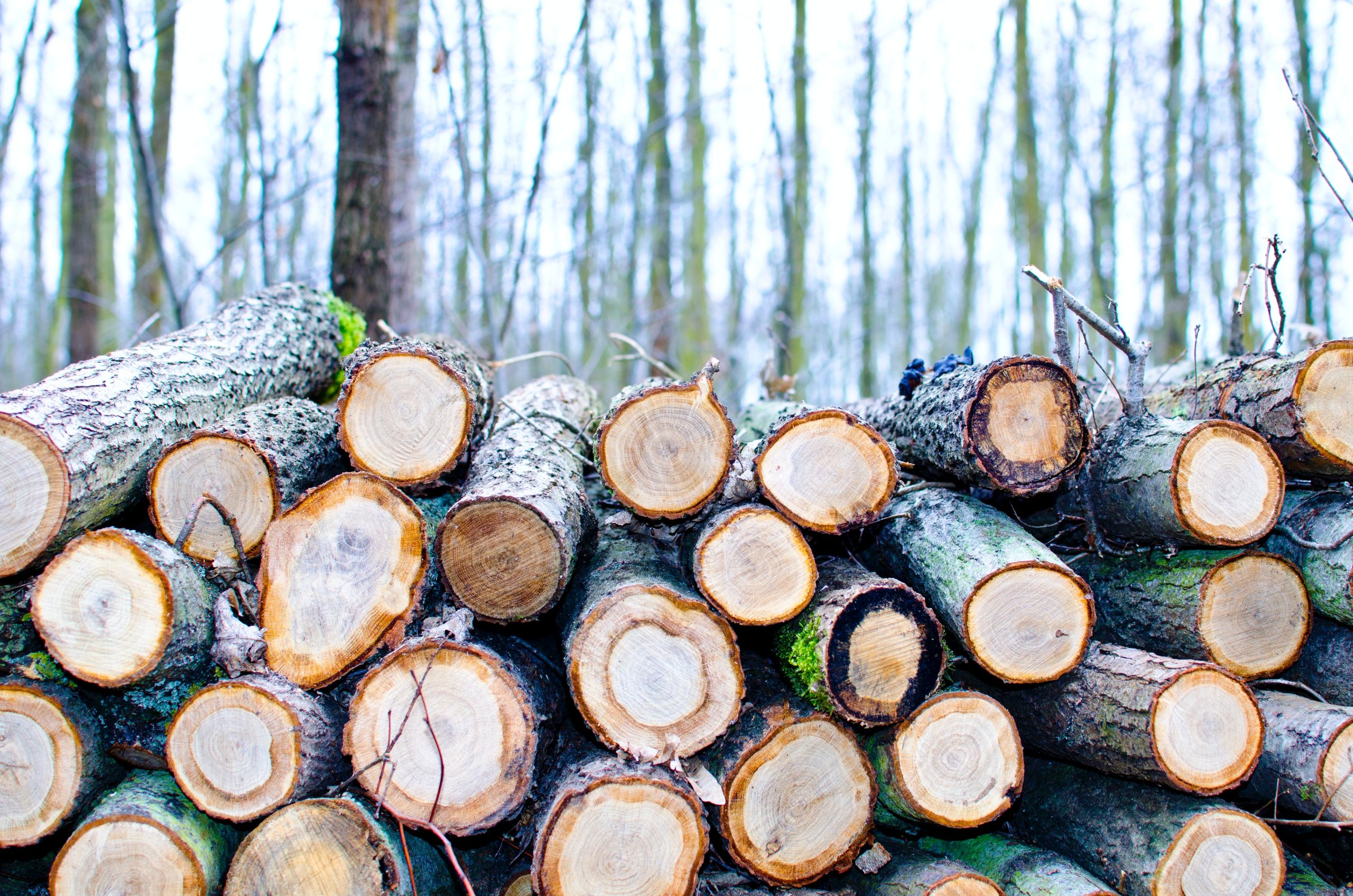
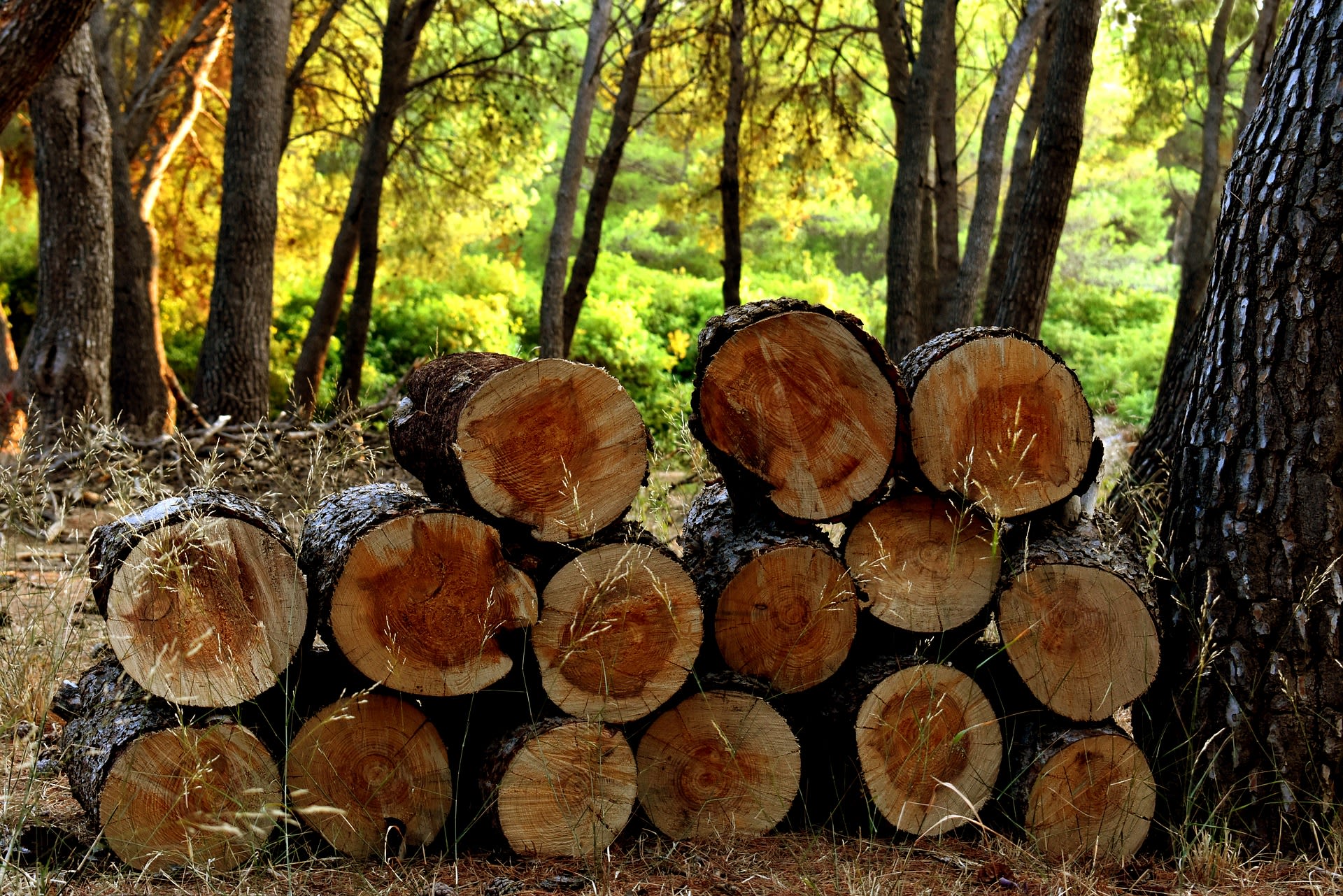
Read the full paper
Kwong, K.; Mao, R.; Scott, S.; Dennis, J.; Marek, E. Analysis of the Rate of Combustion of Biomass Char in a Fluidised Bed of CLOU Particles. Chemical Engineering Journal 2020, 127942.
